How to optimize your warehouse to drive growth and profit
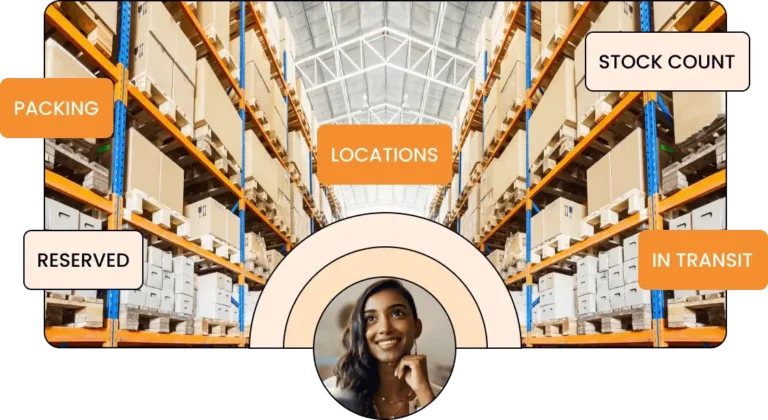
Keep Stock Accurate
Deploy our Warehouse Management Software (WMS). It will simplify and streamline the work of precisely tracking the physical journey of every SKU from receiving to storage and onto outbound shipments.
Drive Optimization with Data
Use data created by the SKU journey to glean insights and take actions that result in lower costs, higher efficiency, and higher customer satisfaction. Continually learn and fine-tune.
Increase Order Volume
To increase revenue and drive repeat orders and order throughput, use ABC analysis to drive up service levels, and implement cycle counting to continuously ensure stock accuracy.
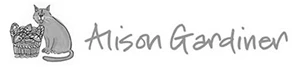
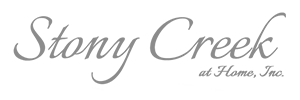
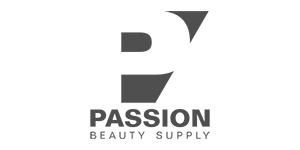
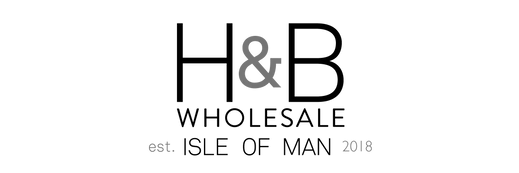
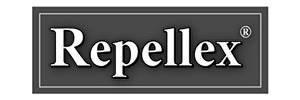
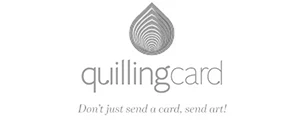
What does our Warehouse Management Software (WMS) do, and how does it drive growth and profit?
Precisely track every SKU Journey
The Salesorder.com WMS enables you to precisely manipulate and track the journey of every SKU from receiving to storage and onto outbound shipments. It uses Barcode scanners to track SKUs. It simplifies and streamlines warehouse tasks. Our WMS is part of the Salesorder.com solution for wholesaler optimization. It requires no integration. It is optional at no cost.
What gets measured gets optimized to drive profit
Our WMS gives you real-time visibility of inventory levels, locations, and movements within the warehouse. This means precise data in reports that empower you with actionable insights to fine-tune processes, optimize inventory levels, and anticipate market trends. This data-driven approach leads to informed decisions to optimize throughput, service levels, and customer satisfaction, which in turn drive growth and profitability.
Increase margins and revenue
An optimized warehouse, finely tuned and meticulously organized, offers myriad benefits that ripple through the entire supply chain, driving efficiency, reducing costs, and enhancing customer satisfaction. These gains inevitably lead to better margins and revenue.
ONE system, one truth. Our WMS is optional and part of Salesorder.com at no extra cost.
Every function in Salesorder, including the WMS, is built on ONE database. ONE source of truth, no integration, no third-party apps (or costs). Everything is unified and real-time.
Multiple warehouses - versatile and no extra cost
You can spin up as many additional warehouses as you need for no extra cost. The Salesorder WMS is versatile and can model different scenarios.
For example:
- A warehouse containing stock not owned by you.
- A 3rd party Warehouse, e.g. Amazon FBA.
- Stock in Containers in transit.
SKU instance tracking - track every individual SKU journey
You can track lots, expiration dates, batches, and SKUs with serial numbers. When you receive any stock in the warehouse, an SKU instance is created. Instances store information about the origin and destination of each SKU.
Using the Stock Manager feature you can review instances to discover which Supplier, which PO, which Customer, and which Sales Order, etc.
Optimize inventory management movements with Barcodes
Using Barcode scanners to track inventory movements eliminates manual errors and minimizes discrepancies.
Barcode scanning is real-time, and therefore, your stock situation is always up to date.
Our Item Master stores SKU Barcode IDs, including Customer and Multipack SKU codes.
We provide a barcode scanner app for Android devices that connects the scanner(s) to the WMS.
Scanner user logins are independent of the main app. You can set permissions for workflows by a user. For example, User 1 can only Pick, User 2 can Pick and Pack, etc. You get the idea.
WMS Console - Configure, Oversee, and Intervene
Each Warehouse has its own dedicated Console. This enables users with permissions to configure features such as user permissions, workflows (i.e. Receiving, Picking, etc), Locations, etc.
WMS Console users can oversee and follow all Barcode operations, for example, the journey of each Shipment and the picking and packing of each SKU.
From the WMS console, users can intervene and take over any task.
Real-Time Event History
Each WMS keeps a detailed log of every event in your warehouse, including the user and task.
Always accurate stock
How to track real-time visibility of inventory levels, locations, and movements in your warehouse(s)
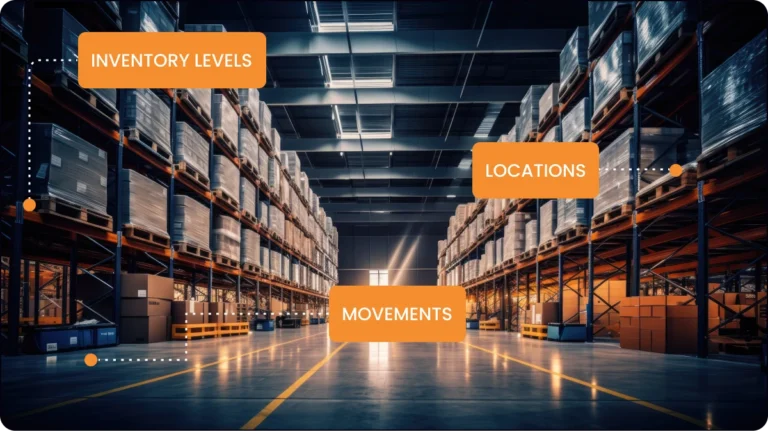
Optimize inventory management with configurable Locations
You can configure WMS Locations to model your layout and tell warehouse workers why, how, and where SKUs are located. You can assign SKUs to one or more Locations. Locations can be configured to support your picking and putaway strategies, pick order, and routes. How a Location is configured can depend upon factors such as demand, SKU status (i.e. In Transit, Quarantine, etc.), Order #, size, weight, and storage requirements.
Examples are:
- Goods In and Out
- ABC locations for high turnover SKUs
- Packing
- In Transit Container
- Building of Kits or Assemblies
- Reserved for specific Orders
- 3rd Party Location
- Reserved Quarantine
- Stock Count Group
- Efficient space utilization not only increases storage capacity without needing physical expansion but also significantly enhances operational throughout
Walkthrough our Warehouse Management System
FAQ
How do you know if you need a warehouse management system?
Here are some indicators that suggest you may benefit from implementing WMS:
Inventory Management Challenges:
- Are you experiencing inaccuracies in inventory tracking?
- Do you struggle to maintain optimal inventory levels or face stockouts and overstocking issues?
- Are manual inventory management processes leading to errors, delays, or inefficiencies?
Order Fulfillment Issues:
- Are order processing times longer than desired?
- Do you face difficulties in prioritizing orders or managing peak demand periods?
- Are order errors, such as incorrect shipments or missing items, common?
Space Utilization Concerns:
- Are you running out of storage space or facing challenges in organizing inventory?
- Do you have difficulty in locating items quickly or optimizing storage locations?
- Are you considering warehouse expansion due to space constraints?
Lack of Visibility and Control:
- Do you struggle to track the movement and status of inventory within the warehouse?
- Are you unable to access real-time data on inventory levels, order status, or warehouse performance?
- Do you face challenges in managing multiple warehouse locations or dealing with inventory across different channels (e.g., e-commerce, brick-and-mortar)?
Operational Inefficiencies:
- Are manual processes, such as data entry and paperwork, slowing down operations?
- Do you have difficulties in managing labor resources effectively or optimizing workflows?
- Are you experiencing high error rates, leading to rework, returns, or customer dissatisfaction?
Scalability and Growth Objectives:
- Are you planning to expand your business, product lines, or warehouse operations?
- Do you anticipate increasing order volumes or complexity in the future?
- Are you looking for a solution that can scale with your business and support future growth?